In almost every industry, various business automation solutions make repetitive tasks more efficient. Technological advancements are transforming daily operations, especially in manufacturing and logistics, with the availability of automatic palletizing systems.
Among the various tasks in the manufacturing and logistics industries, palletizing is repetitive and manual work that puts your workforce at risk for workplace injury. Transitioning into an automatic palletizing system is a simple way to jump-start automation and benefit your business in the long run.
Although adopting the technology requires an upfront investment, the systems offer several benefits ranging from better productivity to increased safety. Sadly, some companies are hesitant to integrate the technology, most often due to concerns about cost and complexity.
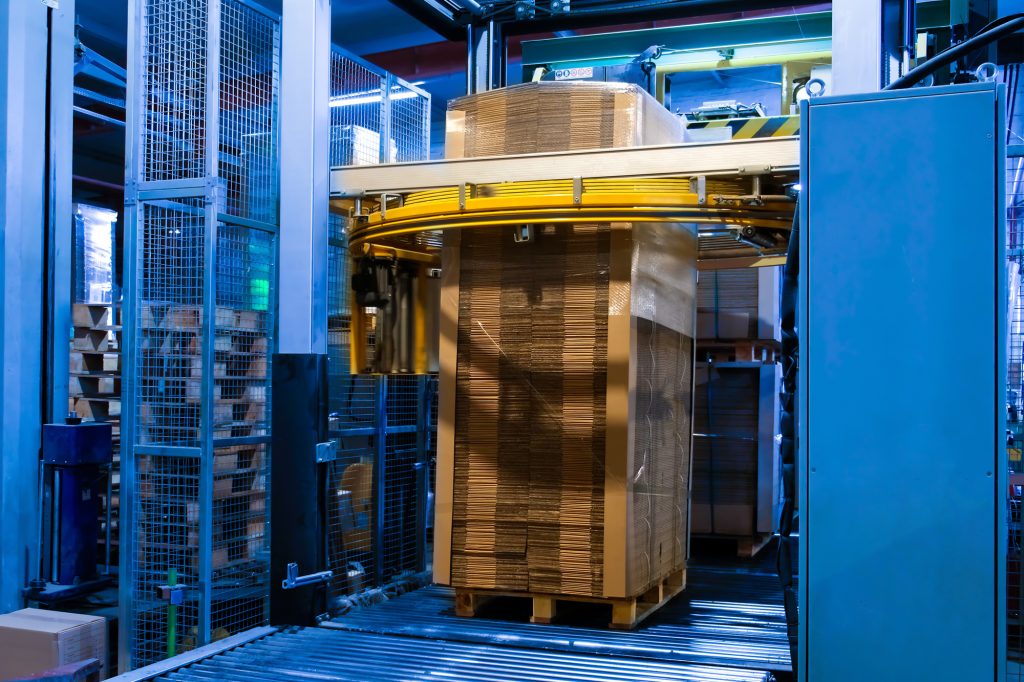
Contents
Understanding Automated Palletizing
A good starting point is knowing the question, “What is a palletizer?” A palletizer is a machine specifically designed to stack products onto pallets in a precise and organized manner. Integrating an automated palletizing system is the key to better efficiency and productivity.
Thus, traditional palletizers work by directing products via a conveyor system. In an automated system, robotic palletizers can stack products onto pallets and even handle depalletizing. A hybrid type is an even more advanced system that combines conventional layer palletizers’ capabilities with robotic arm palletizers’ flexibility and precision. By embracing these innovative systems, businesses can enjoy the full benefits of automated palletizing.
Benefits of Automated Palletizing
Automating daily operations is worth considering if your company wants to maintain an edge. If you’re still undecided about transitioning into an automated palletizing system, here are several benefits it can provide your business in the long run:
1. Better Product Quality
If the pallets are stacked manually, it can often lead to unstable or inconsistent stacks, which may result in the breaking down of the pallets and damage to the products during shipping. The outcome would be dissatisfied customers, returns, refunds, and extra time spent on resolving these issues.
With automated palletizing, you can position your products consistently in the correct place. It depends on your chosen stack pattern, which leads to stable and well-arranged palletized stacks. Doing so lowers the risk of damage during storage and transit. It can also help with stock control since the pallets are consistently stacked.
2. Cost Savings
Transitioning to an automated palletizing system is also key to cost savings. Adopting the approach can reduce the need for manual labor, leading to significant savings on labor expenditures. An automated palletizing system can also work around the clock, which also helps eliminate the need to employ an additional workforce.
A semi-automatic palletizer requires an operator to execute basic tasks such as adjusting the settings. However, other than that, the system can function automatically at every step of the palletizing process. Aside from cutting labor costs, you can repurpose labor by delegating core tasks to employees.
Palletizing also helps cut down the loads per truck while maximizing space. It helps condense several products into a single unit. With fewer units to ship out, it reduces the freight cost, resulting in significant savings for your company.
3. Improved Safety In The Working Environment
Automated palletizing improves the working environment during the production process in terms of safety. Integrating the system eliminates the need for manual handling during palletizing, removing the risk of repetitive strain injuries (RSI) among workers in the workplace. It significantly lowers the risk of RSI claims and ensures a safe working environment for your employees.
The best way to lessen repetitive strain injuries is to invest in equipment that reduces the amount of time spent on handling physically strenuous tasks or eliminates the need for human labor.
4. Eliminates Bottlenecks in the Production Process
In almost any type of industry that utilizes the palletizing process, it’s usually the bottleneck of production. In scenarios where the palletizing task cannot cope with the load, there’s no option but to slow down the production process. Sadly, it leads to lost production time. The right automated palletizing system should accommodate the production process at maximum capacity.
5. Flexible and Adaptable Nature
The increasing availability of automated palletizing is due to the system’s flexibility and adaptability. Modern techniques have configurations and adjustments to readily adapt to changing market demands or product lines. Changes will not involve significant investments in new equipment or machinery.
For example, both automatic and semi-automatic palletizing systems require minimal human intervention. Both are also capable of handling sorting, transferring, and stacking autonomously. The stark difference is that machinery is not injured when performing repetitive motions. In the long run, it leads to a significant drop in injuries in warehouses or production lines.
6. Save or Optimize Available Floor Space
If your current work environment lacks enough space to accommodate bulky machinery, there are palletizing systems that are compact yet highly efficient. A good example is a robotic palletizer that is modular in design.
The compact and modular design allows them to fit into tight spaces easily. If you plan on switching to machines from manual palletizing, it’s crucial to remember that even though the palletizers take up space, they utilize it more efficiently.
7. Boost Productivity
A palletizing system is an effective way to boost productivity in the processing department and warehouse operations. The machinery is capable of swift functioning while maintaining high precision. Essentially, it’s something that humans cannot match. In no time, your company can produce and ship freight in less time with low chances of errors.
Unlike a human workforce, machines are hard-working. Aside from being reliable and having a low probability of making mistakes, machines don’t require days off or sick leave as long as you provide them with routine maintenance. Doing so ensures the production levels stay optimal even when there’s a shortage of workers.
Final Thoughts
The decision to invest in automated palletizing systems would be a practical move. The transition is the key to making processing and warehouse operations more efficient and productive while cutting labor costs. Due to the wide array of automation systems available, it may be best to research all the suitable options and choose one that can cater to your company’s needs. Automating the palletizing task is the best way to achieve efficiency and streamline daily operations.
The Daily Buzz combines the pursuit of interesting and intriguing facts with the innate human desire to rank and list things. From stereotypical cat pictures to crazy facts about the universe, every thing is designed to help you kill time in the most efficient manner, all while giving you something to either laugh at or think about!